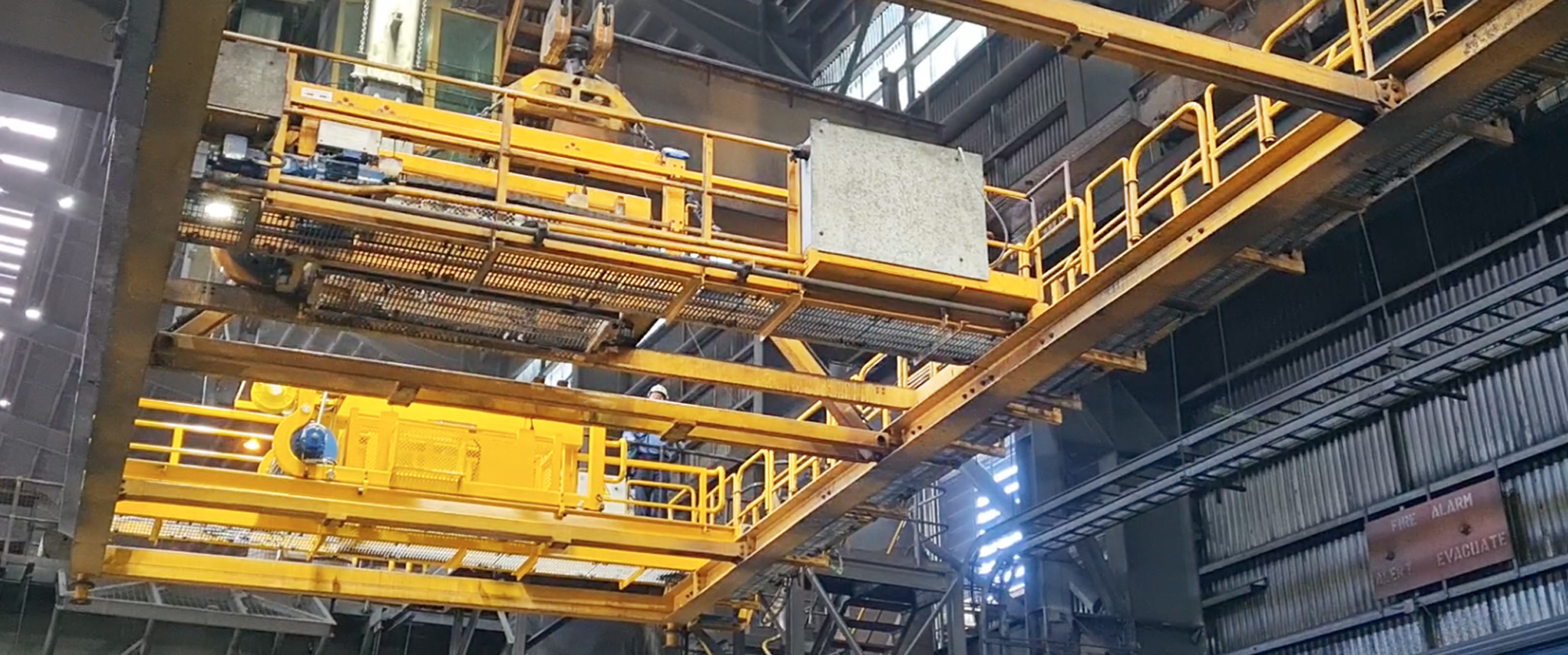
Pit Maintenance Units.
Rio Tinto, Boyne Smelter.
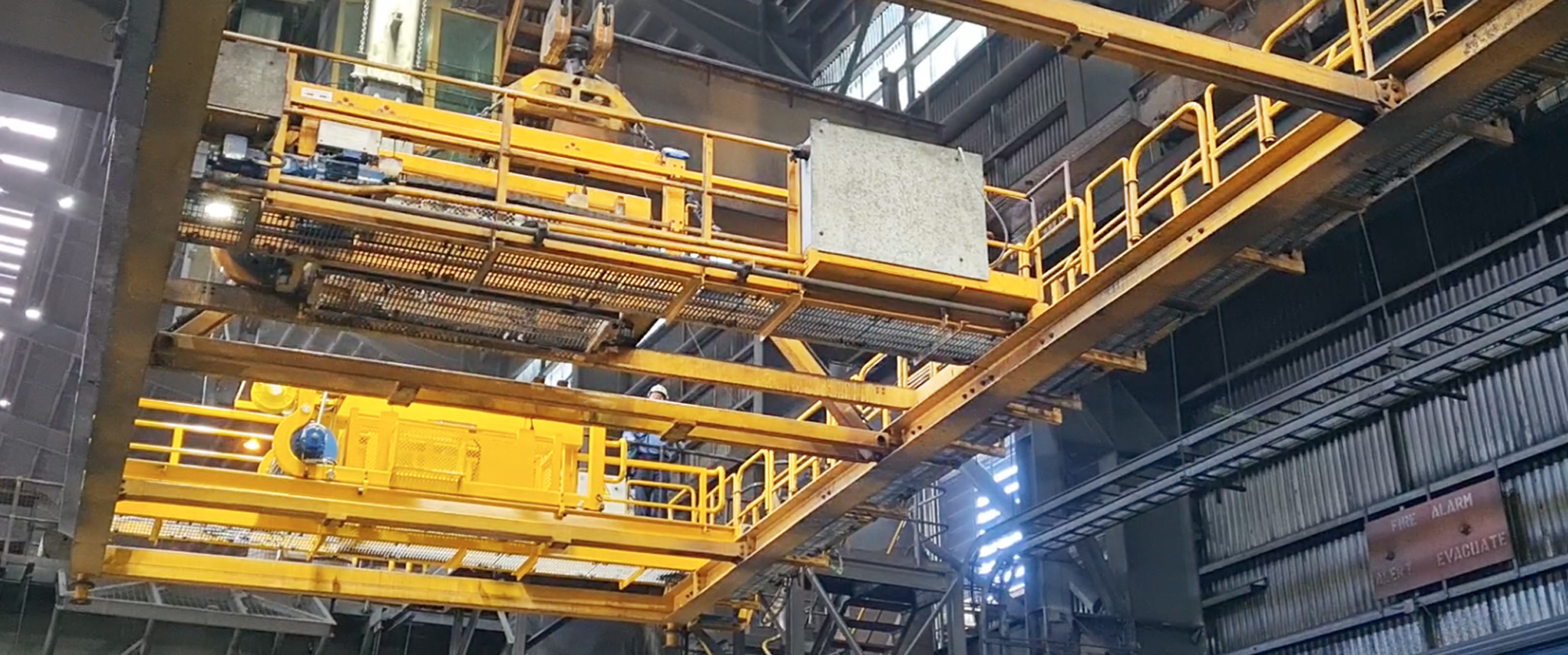
CUSTOMISATION AND SAFETY IN ALUMINIUM SMELTERS.
RIO TINTO ALUMINIUM SMELTER, AUSTRALIA.
PROJECT
Following the successful installation of a Farra Pit Maintenance Unit back in 2012 the Boyne Smelter required the design and manufacture of an additional Pit Maintenance Platform (PMP) for the carbon bakehouse CBF3 at Boyne Aluminum Smelter.
ROLE
Each Carbon bakehouse environment tends to have its own unique working environment and challenges. In this case, we needed to come up with a low-profile unit to work around the lower-than-unusual maintenance hook heights. It had to be able to lift over the central conveyor.
Team Farra designed and manufactured a PMP that was similar to the existing model with improved safety and operational features as part of an ongoing development program. The bespoke PMP fit securely over 8 pits enabling safer, easier and faster access to the carbon bake pits for routine maintenance of the flue walls. This long travel gantry, short travel crab and descending cage. The dual gantries provide access to adjacent pits and park symmetrically to provide a perfectly balanced machine for single-point lifting. This is user-friendly and means workers can be relocated to the next set of pits as quickly and efficiently, driven by the reliability of the bespoke hoists, that we have developed over the years for both the PMU and BMU Access Machine market.
RESULTS
We have a long-standing relationship with Rio Tinto worldwide with several Farra PMUs in their Aluminium Smelter. Rio Tinto was highly satisfied with the solution and the highly responsive service, commissioning this unit in just 2 days, which was much less than the expected 5 days downtime.
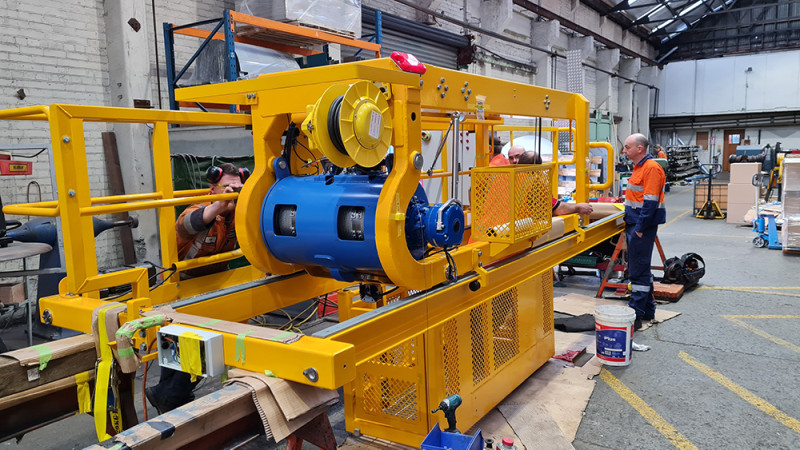
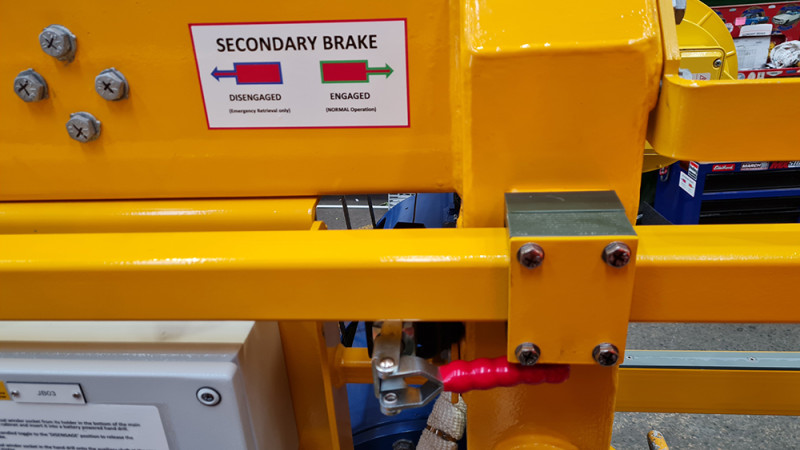
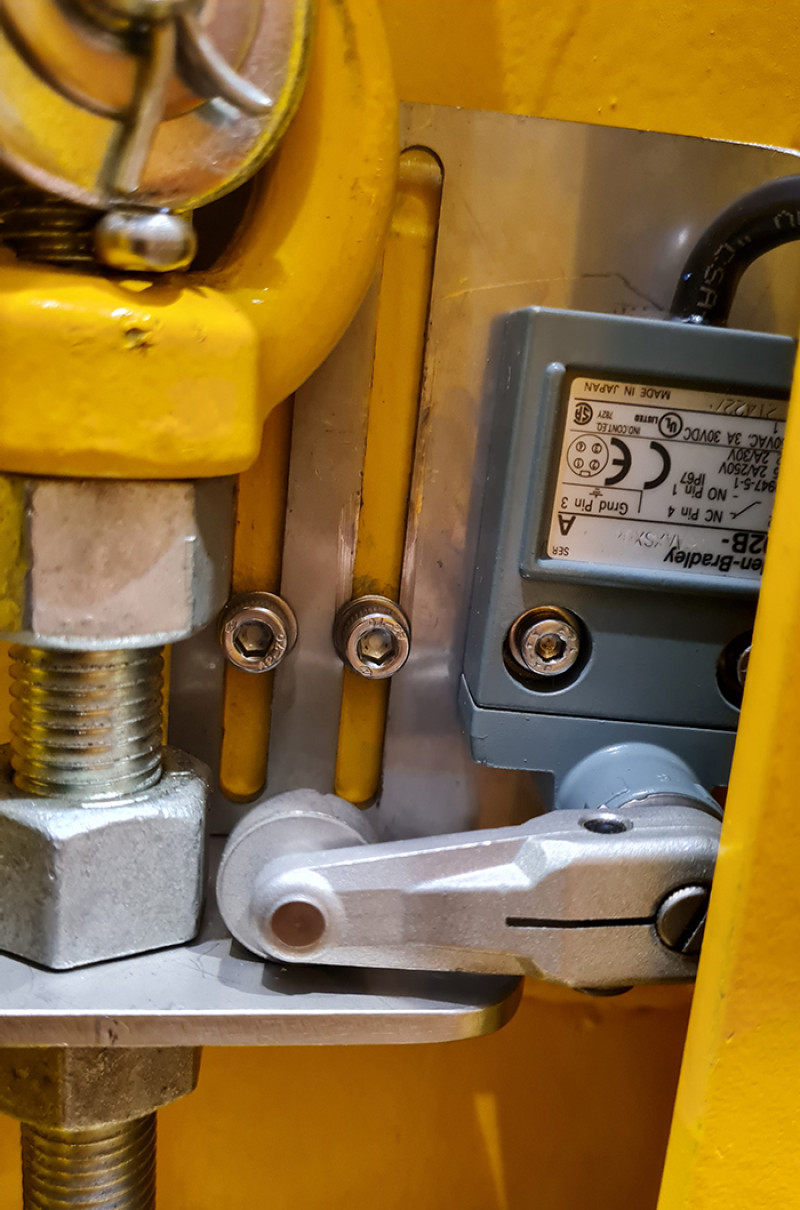
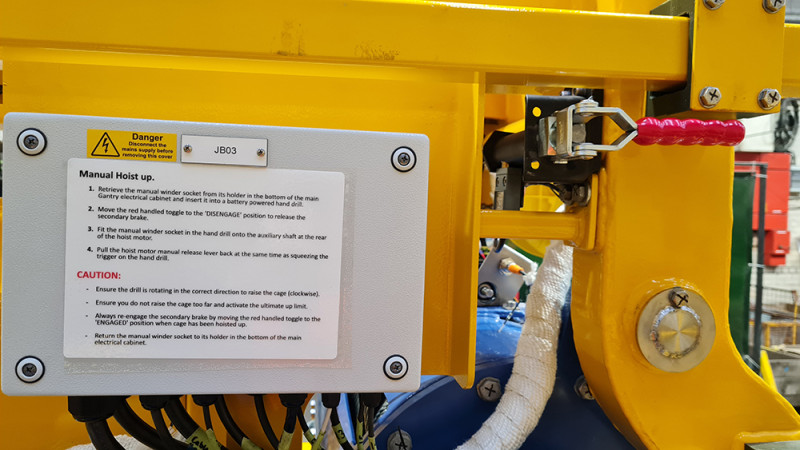
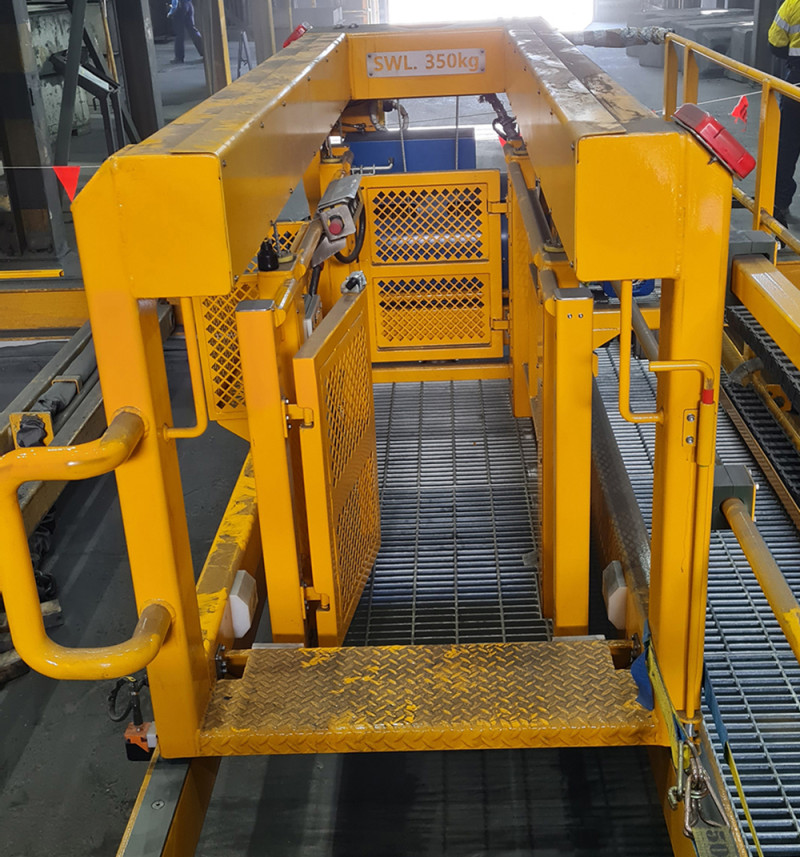