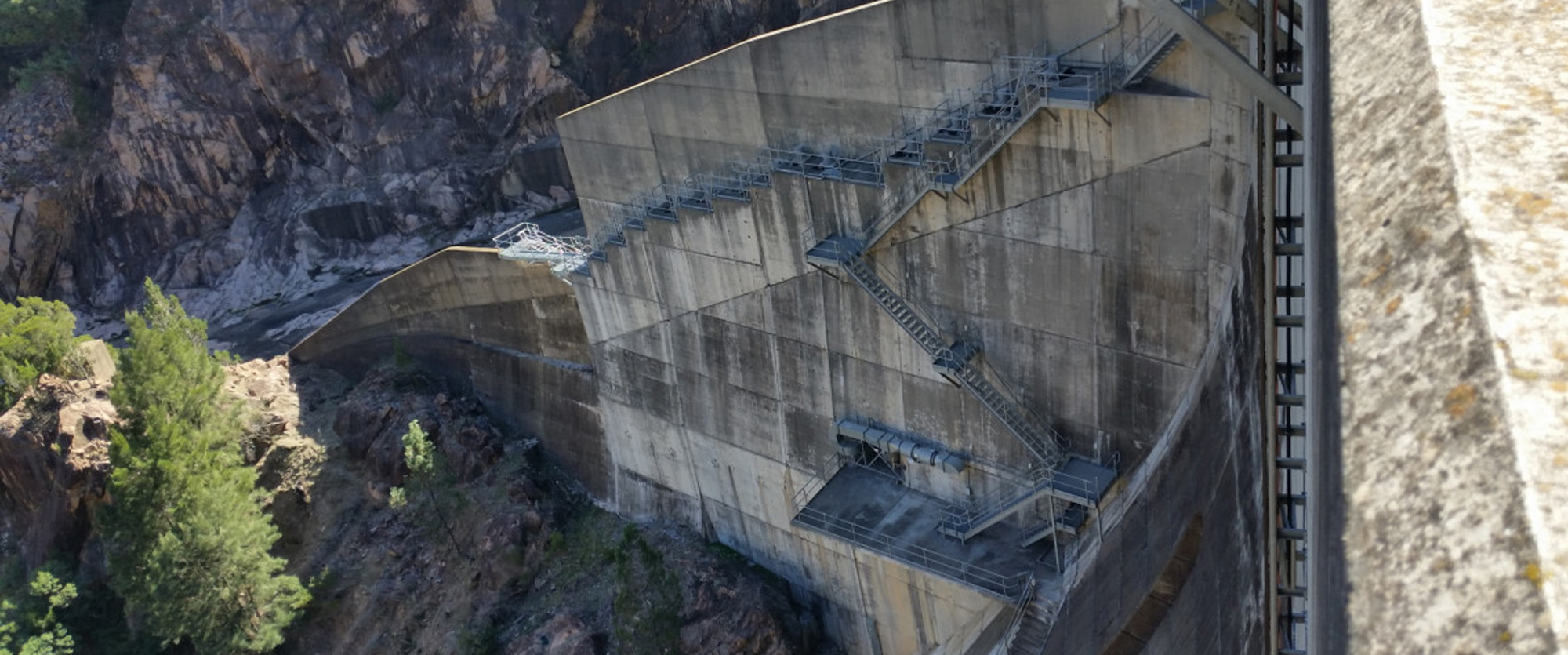
Turbine refurbishment.
Burringjuck Station
Portable Borer for Main Inlet Valve.
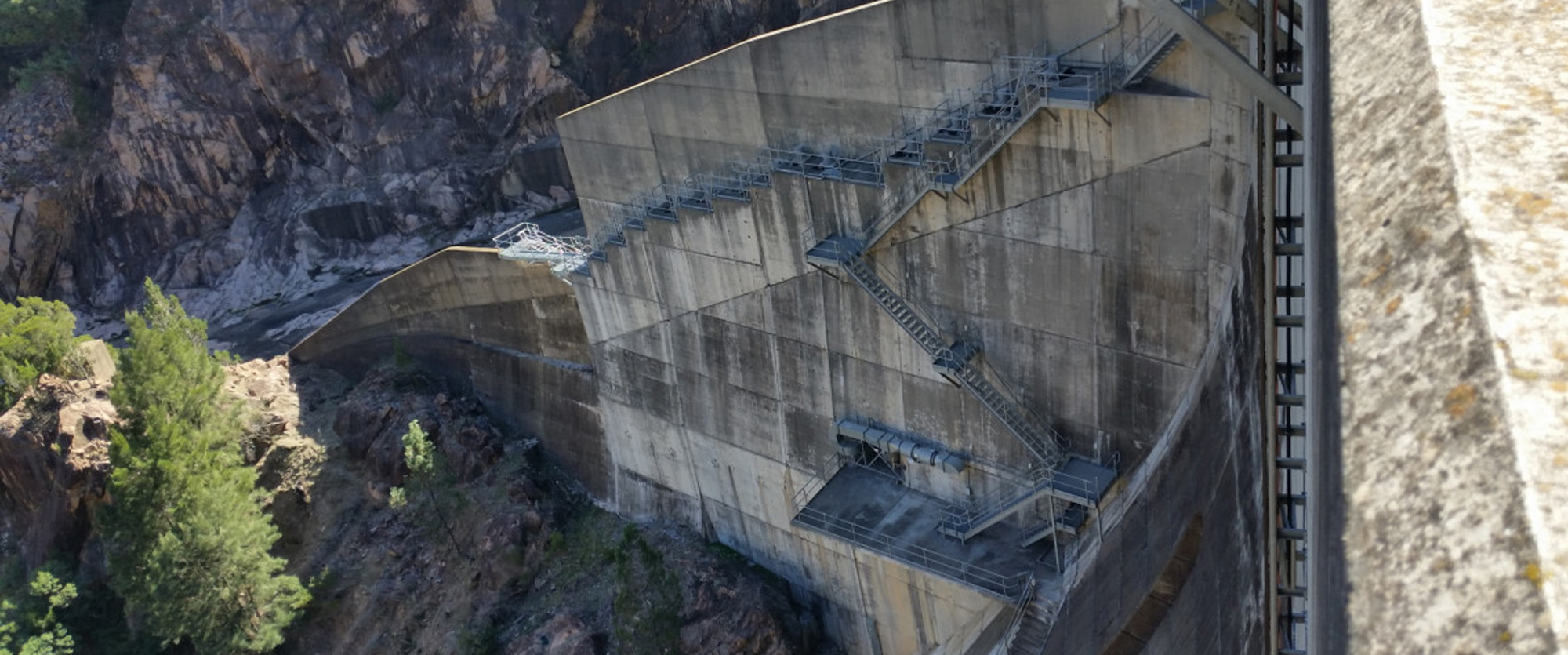
TAKING ON THE IMPOSSIBLE.
A BESPOKE MIXED METALS COMPACT BORING MACHINE FOR BURRINJUCK DAM.
PROJECT
Located in Burrinjuck National Park near Canberra, Australia, this Hydropower Station was a challenging project. The radial dowels connecting the control arm to the butterfly valve body had become worn with the risk of failure. Many companies deemed refurbishment of the Main Inlet Valve (MIV) drive dowels in-situ as impossible. Access was limited via manhole and they were recommending a complete replacement, which would be in the tens of millions. There was a resounding ‘Call Mike at Farra’.
ROLE
Team Farra came up with a bespoke compact high-precision boring machine to repair the valve with consideration to the complexities of:
- A location with restricted access.
- Working in confined spaces and limited work space to complete the project.
- Producing a parallel, straight and round borer with a 0.02mm tolerance, that can bore through half 431 stainless steel and the other half low carbon steel.
Location and Access Challenges
The first location hurdle was the access to the building housing the MIV. Down a two-man lift the size of a phonebox that descended the face of the dam, or hundreds of stairs that wound their way down to the bottom of the dam. The manhole sized entrance hatch was the only way into where we needed to be, the penstock tube. The access and physical valve body construction eliminated any standard OEM supplied equipment as part of the solution.
Borer Design
The borer that was small and light enough to fit within the access restrictions but powerful and precise enough to bore through the low-carbon steel of the control arm and valve body, and the stainless steel of the connecting shaft. Boring 250mm deep through two different types of metals. To guarantee that precision on-site, the team in the machining workshop tested the borer to 0.01mm. Ensuring 0.02mm tolerance when it came to on-site implementation. The team and the borer worked perfectly onsite, within 0.015mm.
RESULTS
The client was very happy, saving a fortune and refurbing a machine meant they could conduct themselves in a much more sustainable way for this project. The borer has also been used at their other locations. Mike Ryan was recognised in 2023 for his Leadership in Engineering on this project and others like it at the HERA industry body awards.
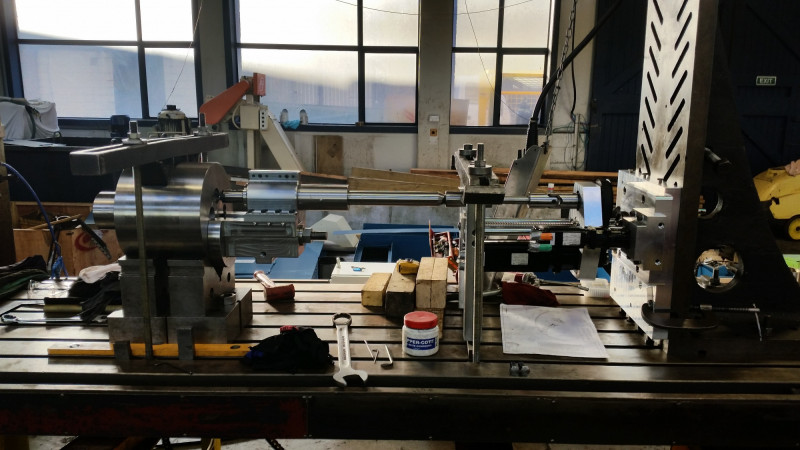
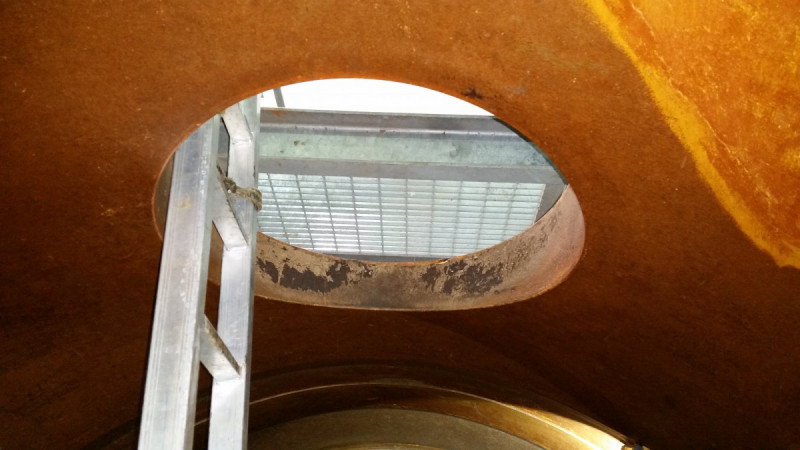
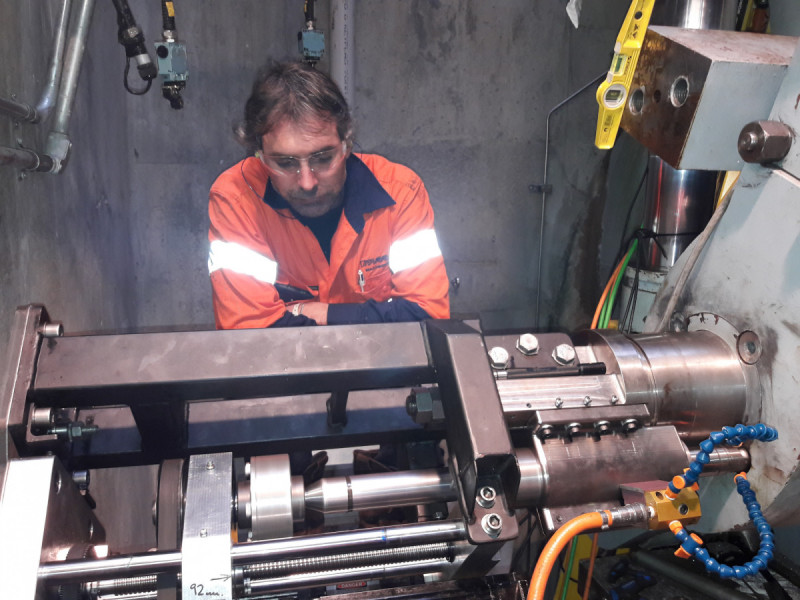
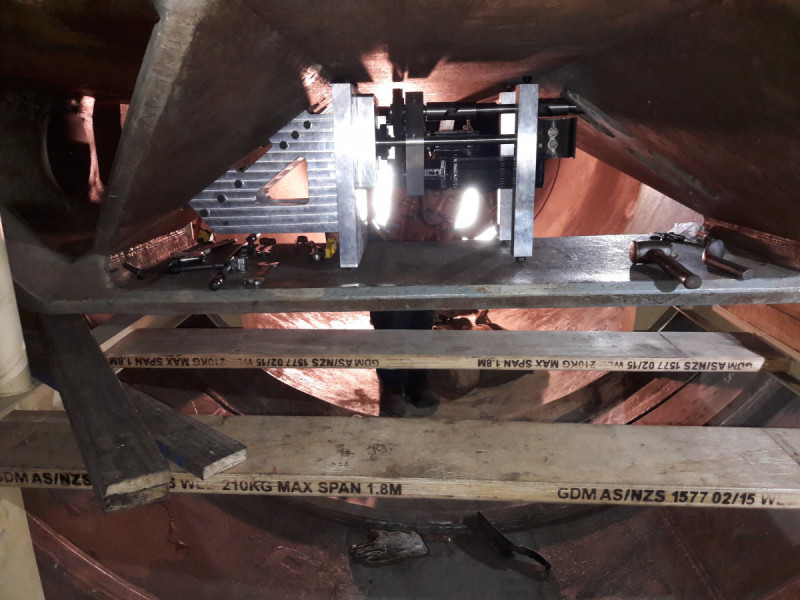
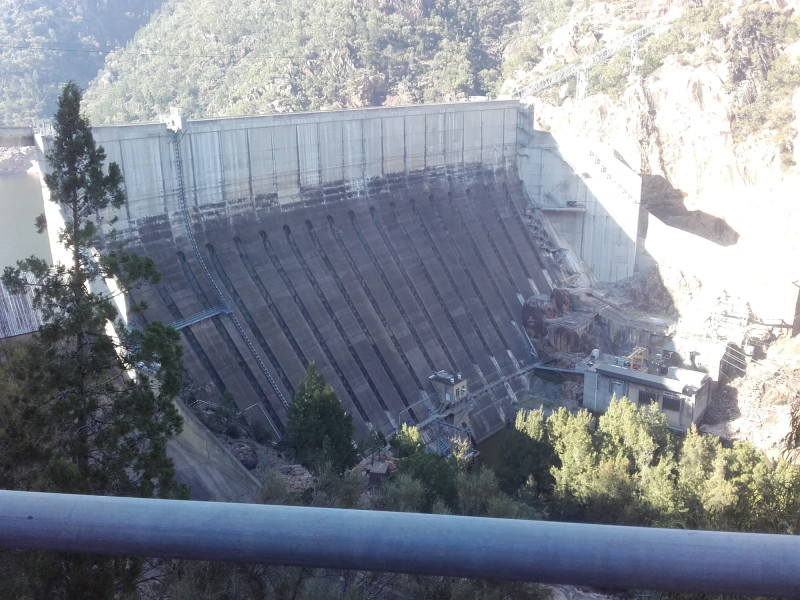